Raben Logistics Polska is characterized by a wide range of logistic solutions tailored to the individual needs of customers from various industries. As part of the service, the company carries out transport projects of varying complexity, including co-manufacturing and co-packing services, such as: product packaging, repackaging for retail chains, production of sets and combining products, product labeling and management of production components. In 2021, the company received an award as part of the 20th edition of the Logistics Operator of the Year survey in the category "The highest standard of delivery service on the market" and a special award "The most efficiently managed logistics company".
Challenges faced by the project
Due to the intensive development of the service segment and the growing customer requirements, the company was looking for tools that would allow, among others: efficient use of resources, automating and systematizing the planning process, real-time monitoring of production efficiency, automation of production quality management and the development of issues related to the traceability of raw materials and components for the manufactured unit. The solution proposed by eq system included both the implementation of the MES class system and the ASPROVA APS production planning and scheduling system.
- For us, the implemented ASPROVA and MES systems are not independent entities, but support our main WMS system in planning, information flow and production execution. We were well aware that only the implementation of both systems at the same time would bring the expected results - says Łukasz Dubina, Value Added Service Director at Raben Logistics Polska. - The first and basic goal was to get the production from the warehouse on time with the maximum reduction of the buffer space before and after production.
Comprehensive production management
- A detailed plan is sent to WMS from ASPROVA, when, which and in what form the logistic unit is to be delivered from the warehouse so that its stay in the buffer is as short as possible or which is to go directly to the production station. MES, in turn, manages the execution of this plan, the technology of execution, manages the quality plan and guards the traceability and production costs. From our perspective, there was no justification for separating the implementation of both systems, explains Łukasz Dubina.
Currently, after receiving information from the client, the planner in ASPROVA APS has the ability to reserve resources for a future order and assign a specific route to them, according to which the resources are planned and the future order will be implemented.
If a similar route has been previously defined (e.g. the index is ordered again or a similar index was produced), ASPROVA refers to it automatically. Then the details are determined: material balance and availability control of the structure components (based on the product structures defined by customers and auxiliary component structures on the part of Raben Logistics). BOMs built by the planner in the ASPROVA APS system are communicated with the WMS. At this stage, the planner waits for the client's physical order, which is sent to ASPROVA through the WMS system, where it is automatically allocated over a specific period of time through the identification system.
For new productions, technological details are defined in the following steps: versions of the batch number used for production, types of logistic labels for manufactured units, quality control structure (standard or extended). Offer data are entered, such as the assumed production standard (specifying the time in which the unit will be made), the price from the offer and cost components. Communication between the WMS and the ASPROVA APS system at the level of a given order enables the planner, even before the start of production, to finally verify whether the date of completion specified in the order is achievable, and whether the necessary raw materials and components are available. In the case of identifying the lack of components for production, the planner is given the opportunity to react immediately and introduce changes. In the planning process, ASPROVA enables the analysis of the work of not only typical production teams, but also precise planning of the work of forklift truck operators, the most limited resource at the interface with warehouse operations.
- Due to the fact that we operate in the distribution warehouses of our clients, rescheduling occurs quite often. Before the implementation of ASPROVA, we had to apply all the changes to the plans made in Excel, and the rescheduling process consumed a lot of time of key people in production. Currently, we can operate according to various planning scenarios embedded in the planning process, optimizing the use of resources. What's more, in the ASPROVA system we have gained the ability to reserve resources "ahead of customers' signals." - adds Łukasz Dubina.
Implementation of the "just in time" strategy
- What we put a lot of emphasis on was the level of ASPROVA's integration with WMS. The result of planning is a detailed production schedule for all workstations, in which it is extremely precisely defined what and when is to appear in the production area. We have great flexibility in the definition of a logistic unit for individual production components, which is moved from warehouse inventory. It can be a piece, a box, a layer or a whole pallet. Previously, we allocated large amounts of materials from the warehouse to production lines, corresponding to entire orders, today, thanks to the ability to plan in time, we have become "just in time", adjusting the development of subsequent pallets in a cycle convenient for us. We have reduced the space used for component buffers to a minimum, thus increasing our production space. This is one of the most important implementation results for us, explains Łukasz Dubina.
The queue of operations resulting from the planned production orders, indicating the planned start / end time and the resource / position on which the operation will be performed, is imported from the ASPROVA APS to the MES system. Also attached is a technical plan for the production line, how it is to be built, specifying the number of people and capacity required. The foreman from the production terminal level starts the visualization, thanks to which he has full access to the line documentation with photos. All relevant information about the production progress and related material transactions registered in MES are transferred to WMS and ASPROVA APS.
Product genealogy guarantees high quality
Raben Logistics Polska customers have a constant online view both to the inventory of components and final products, as well as to individual production activities, such as moving pallets with components, or the creation of individual pallets of the finished product.
Very important is the aspect of ongoing access to quality records, confirmed by the quality control team with photo documentation during production processes, ie "golden sample" (the first production unit that is assessed for compliance of performance), assessment of technical aspects of production and palletization of goods. Additionally, in the case of full EDI system integration between Raben and the customer, each point important for inventory management is reflected in a message to the customer's ERP system. Information confirming the production of a finished product is generated pallet by pallet for a given order, and additionally it can be supported with a message about the disposal of individual components for a given pallet.
- Providing service at the highest possible level is one of our priorities. The transparency of the process and the disclosure of information, also regarding quality control, means for the customer the certainty that he is cooperating with a trustworthy company - says Ł. Dubina. - With a company that will guarantee him that his production is not endangered, both in terms of the deadline and the quality of workmanship.
Traceability is fully implemented in Raben Logistics Polska. Communication between WMS and ASPROVA APS and MES ensures tracking to the level of a unit defined in the process - usually a pallet or a display. Starting from the acceptance of the pallet to the WMS, the systems communicate with each other, exchanging information identifying individual logistic units of goods. Data generated in MES on newly created units are returned to the WMS with the full traceability history of their components.
In myRaben application, the customer has access to the entire history of the batch: receipt, production (which pallet, with which goods were made from the batch, how many units were created with a specific code, with which order it was returned to the warehouse), transport (to which recipients the batch left). Tracking is provided in real time so that the customer has constant access to information about the flow of goods.
Cost optimization
One of the results of the implementation - apart from the maximum use of available space, optimization of resources and increasing employee productivity - is the cost analysis of individual production. The system enables multidimensional data analysis both during and after production, regarding the efficiency of resources (machines and employees), shortages and their causes, downtime, real changeover times and production times. As a result, Raben Logistics Polska is able to increase the volume of transactions and reduce their cost. Better management of the production scrap level by selecting the appropriate power supply unit for the production line, or the analysis of the causes of component damage, also positively affects the cost level of the production.
- For us, the measurable result of the implementation of the MES and ASPROVA APS system is the OTIF indicator, which exceeded the assumed target and currently amounts to 99.88% (counted to the level of a pallet unit), i.e. we produce on time and in the quality expected by the customer. We must not forget that the market, especially in the value added services segment, will change rapidly. Thanks to the synergy between the APS, MES and WMS systems, we are ready for future challenges - concludes Łukasz Dubina.
Implementation goals: | Effects of cooperation: |
|
|
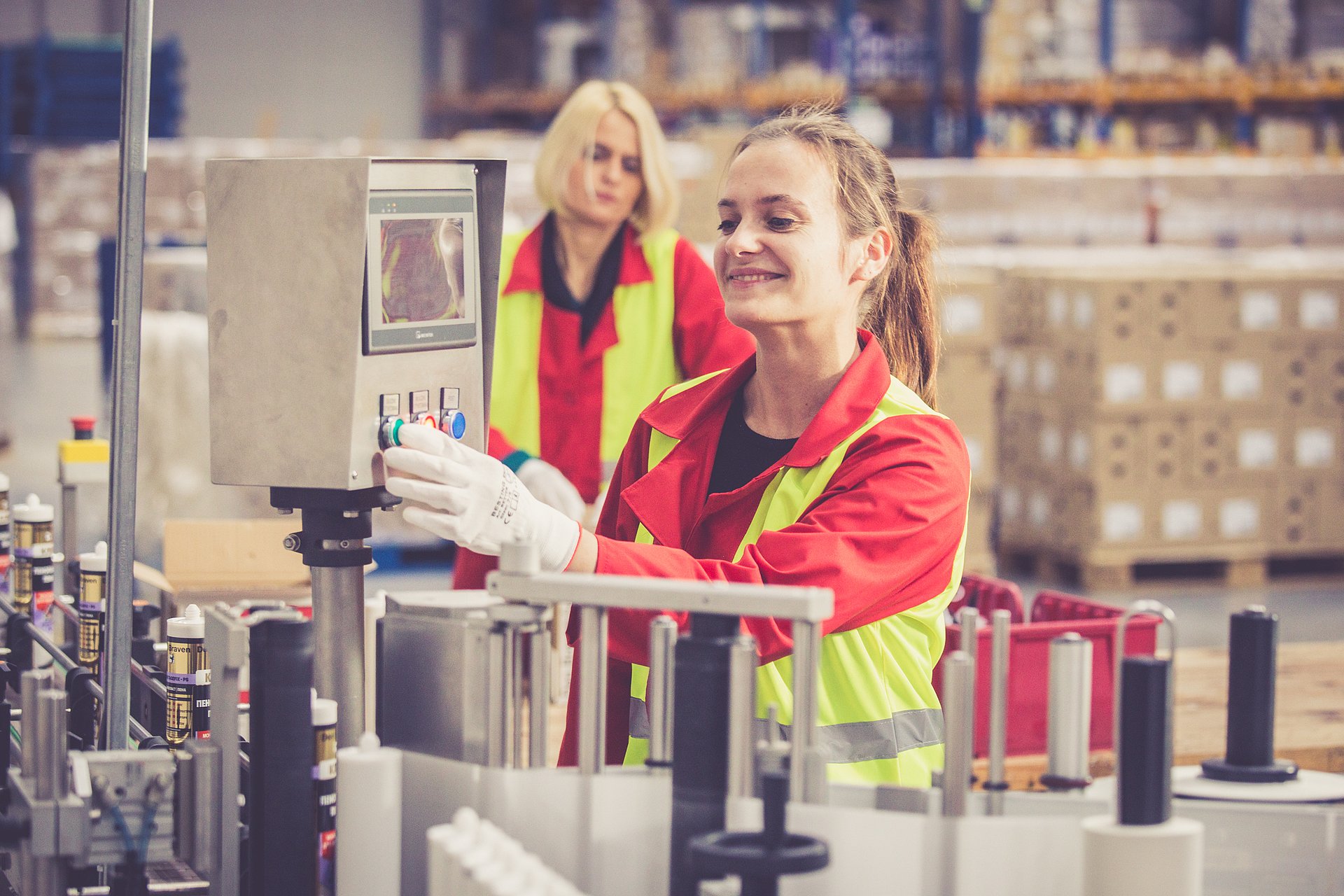